Introduction
CAN Bus Wiring is a crucial component in modern automotive and industrial systems. It allows for the transmission of data between various electronic devices, such as sensors, actuators, and control units.
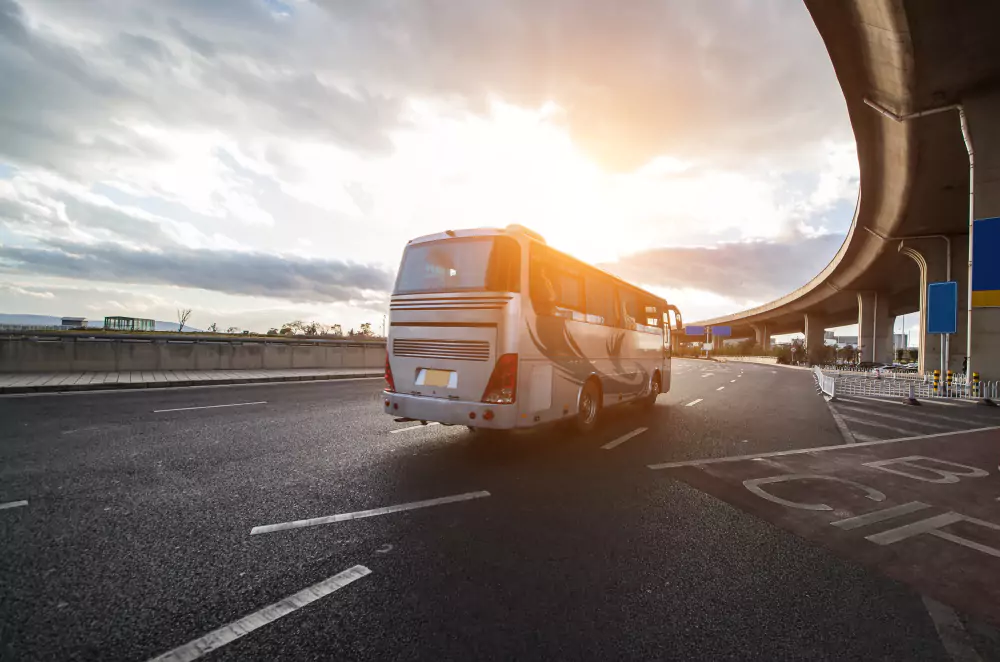
Understanding CAN Bus Wiring is essential for technicians and engineers working with these systems, as it ensures proper installation, troubleshooting, and maintenance.
Understanding the Basics of CAN Bus Wiring
CAN Bus Wiring, or Controller Area Network Wiring, is a communication protocol used in vehicles and industrial applications to enable the exchange of data between different electronic devices. It consists of a twisted pair of wires that connect various nodes in the system. The data is transmitted in the form of electrical signals, which are interpreted by the receiving devices.
CAN Bus Wiring works on a principle of differential signalling, where the voltage difference between the two wires determines the value of the transmitted data. This allows for reliable and noise-resistant communication, even in harsh environments. The system uses a bit-wise arbitration mechanism to prioritize messages and ensure that there are no conflicts during transmission.
One of the main advantages of using CAN Bus Wiring is its ability to support multiple devices on a single network. This reduces the amount of wiring required and simplifies the overall system design. Additionally, CAN Bus Wiring is highly reliable and fault-tolerant, thanks to its error detection and correction mechanisms. This makes it ideal for applications where safety and reliability are critical.
Components of a CAN Bus System
A typical CAN Bus system consists of several key components that work together to enable communication between devices. These components include:
1. CAN Bus Controller: The controller is responsible for managing the communication on the bus. It controls the transmission and reception of data, as well as the arbitration process. The controller also handles error detection and correction.
2. CAN Bus Nodes: Nodes are the devices connected to the bus that send and receive data. They can be sensors, actuators, or control units. Each node has a unique identifier, which is used for addressing and prioritizing messages.
3. CAN Bus Transceiver: The transceiver is responsible for converting the electrical signals from the controller into a format that can be transmitted over the bus. It also amplifies the signals received from the bus and sends them to the controller.
4. CAN Bus Terminator: The terminator is a resistor placed at each end of the bus to prevent signal reflections. It ensures that the electrical signals are properly terminated and reduces the risk of data corruption.
Types of CAN Bus Wiring
There are two main types of CAN Bus Wiring: single-wire and dual-wire.
1. Single-wire CAN Bus Wiring: In a single-wire configuration, only one wire is used for communication. This wire carries both the data and power supply for the devices on the bus. Single-wire CAN Bus Wiring is commonly used in automotive applications, where space and weight constraints are important.
2. Dual-wire CAN Bus Wiring: In a dual-wire configuration, two wires are used for communication. One wire carries the data, while the other wire is used for power supply and ground. Dual-wire CAN Bus Wiring is typically used in industrial applications, where longer distances and higher data rates are required.
CAN Bus Wiring Standards and Protocols
CAN Bus Wiring follows certain standards and protocols to ensure compatibility and interoperability between different devices and systems.
1. Wiring Standards: The most widely used standard for CAN Bus Wiring is ISO 11898, which defines the physical layer and electrical characteristics of the bus. It specifies the voltage levels, bit rates, and connector types for different applications. Other standards, such as SAE J1939 and CANopen, are also commonly used in specific industries.
2. CAN Bus Wiring Protocols: The protocol used for data transmission on the bus is defined by the higher layers of the CAN protocol stack. The most common protocol is CAN 2.0, which supports both standard and extended frames. Other protocols, such as CAN FD (Flexible Data Rate), allow for higher data rates and larger payload sizes.
Common Problems with CAN Bus Wiring
Despite its reliability, CAN Bus Wiring can still experience issues that can affect the performance of the system. Some common problems include:
1. Electrical interference: CAN Bus Wiring is susceptible to electrical noise and interference from other sources, such as electromagnetic fields and power supply fluctuations. This can lead to data corruption and communication errors.
2. Incorrect wiring: Incorrectly connecting the wires or devices on the bus can cause communication failures and malfunctions. It is important to follow the proper wiring diagrams and guidelines provided by the manufacturer.
3. Faulty components: Faulty or damaged components, such as the controller, transceiver, or nodes, can disrupt the communication on the bus. Regular inspection and testing of the components can help identify and replace any faulty parts.
Troubleshooting CAN Bus Wiring Issues
When troubleshooting CAN Bus Wiring issues, it is important to follow a systematic approach to identify and resolve the problem. The following steps can help in the troubleshooting process:
1. Identifying the problem: Start by gathering information about the symptoms and any error messages or codes displayed by the system. This can help narrow down the possible causes of the issue.
2. Testing the system: Use diagnostic tools, such as CAN Bus analyzers or oscilloscopes, to monitor the signals on the bus and check for any abnormalities. Test each component individually to determine if it is functioning correctly.
3. Fixing the issue: Once the problem has been identified, take appropriate measures to fix it. This may involve replacing faulty components, reconfiguring the wiring, or updating the software/firmware of the devices.
Best Practices for CAN Bus Wiring Installation and Maintenance
Proper installation and maintenance of wiring are crucial for ensuring reliable and efficient operation of the system. Some best practices include:
1. Proper installation techniques: Follow the manufacturer’s guidelines and wiring diagrams when installing the CAN Bus Wiring. Use high-quality cables, connectors, and terminators to minimize signal loss and interference. Avoid routing the wires near sources of electrical noise, such as power cables or motors.
2. Regular maintenance: Inspect the wiring and components regularly for any signs of damage or wear. Clean the connectors and terminals to ensure good electrical contact. Perform periodic testing and calibration of the system to detect any potential issues before they cause major problems.
3. Importance of following standards and protocols: Adhere to the relevant standards and protocols when designing, installing, and maintaining the CAN Bus Wiring. This ensures compatibility and interoperability with other devices and systems. It also helps in troubleshooting and resolving any issues that may arise.
Conclusion
In conclusion, understanding CAN Bus Wiring is essential for technicians and engineers working with automotive and industrial systems. It enables reliable and efficient communication between devices, ensuring proper operation and control. By following the proper installation techniques, adhering to standards and protocols, and performing regular maintenance, the performance and longevity of the CAN Bus Wiring can be maximized.